Tungsten Copper Heat Sink Applications
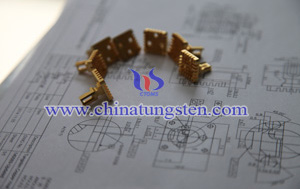
Tungsten copper heat sink works well in densely packed circuits, because of tungsten copper's thermal conductivity and expansion characteristics.Applications of Tungsten Copper Composites WCu Alloy) the manufacturing process of WCu alloy is to press the refractory, sinter the pressed compact at a high temperature, and infiltrate with copper. All of this is done under very closely controlled conditions. The mechanical and physical properties of WCu alloy vary with composition. The combination of tungsten copper materials results in thermal expansion characteristics similar to those of silicone carbide, aluminum oxide, and beryllium oxide, used as chips and substrates.
Resistance welding the high physical and mechanical properties, as well as the thermal and electrical conductivity, of refractory metal composites make WCu alloy very suitable for die inserts and electrode facings, flash and butt welding dies, and hot upsetting. They can also solve heat balance problems. Heat sink the CuW75 tungsten copper alloy is used extensively in thermal mounting plates, chip carriers, flanges, and frames for high-power electronic devices. As a tungsten copper material, it's a composite, so both the thermal advantages of copper and the very low expansion characteristics of tungsten can be utilized. The combination of these two materials results in thermal expansion characteristics similar to those of silicone carbide, aluminum oxide, and beryllium oxide, used as chips and substrates.
WCu composites are made by infiltrating, under vacuum, uniform controlled porous blocks of tungsten with molten copper. This results in a heat sink of lower density, low CTE and excellent thermal conductivity. Bonded fin heat sinks are a common type of heat sinks in today's thermal applications. The primary advantage of bonded fin heat sinks is the fin height to fin gap ratio can be much greater than the maximum ratio seen in extruded heat sinks. For this reason, bonded fin heat sinks can either have longer, taller, fins, or tighter fin spacing than extruded heat sinks. A secondary advantage is that bonded fin heat sinks can be made of aluminum, copper, copper-tungsten, or a combination of these materials. This allows the engineer to balance requirements such as weight, performance, thermal expansion, and cost, to design the ideal heat sink solution for a particular thermal problem.
Our tungsten copper composites to be used extensively in thermal mounting plates, chip carriers, flanges, and frames for high-powered electronic devices. With the thermal advantages of copper with the very low expansion characteristics of tungsten, tungsten copper has properties similar to those of silicone carbide, aluminum oxide, and beryllium oxide. The thermal conductivity and low expansion also make tungsten copper alloy an excellent choice even for extremely dense circuits.